Machinery Failure Expert Witness
Mechanical Forensic Engineers for Machinery Failure -Australia Wide Service
Machinery failure often occurs on the site where the machines are working. Our forensic mechanical engineers will travel to the site to inspect the failed machine where the incident happened. After the inspection, our mechanical engineers will analyse the evidence and determine the root cause of the failure.
The experts at Gilmore Engineers are experienced in the investigation of failures in heavy machinery such as SAG mills, drilling rigs, rock hammers, haul trucks, excavators and large engines used to power trucks, plant and marine vessels.
For 30 years plus, Gilmore Engineers have shown themselves to be a leader in incident investigation and analysis. Over this time Gilmore Engineers has provided over 1,500 reports to lawyers, members of the legal profession and loss adjusters for matters before District, Supreme, and Federal Courts.
Gilmore Engineers will examine the available evidence and give you an initial engineering assessment in the form of a verbal opinion. If necessary, this opinion can be provided in the form of a comprehensive report for the Court. Our experts will then follow through by presenting their evidence to the Court in person on your behalf if required.
Gilmore Engineers is a mechanical engineering consultancy firm in Brisbane with experience in machinery failure. Contact us to discuss your situation.
Machinery Experience
Earth Moving & Farm Equipment
Mining Equipment & Mills
Large Engines
Machinery Attachments
- Dump Trucks
- Excavators
- Graders
- Dozers
- Wheeled Loaders
- Tractors
- Conveyors
- Haul Trucks
- SAG Mills
- Drill Rigs
- Ball Mills
- Truck
- Plant
- Marine Vessels
- Generators
- Rock Hammers
- Hydraulic Rock Grabs
- Hydraulic Log Grabs
- Machine Buckets
- Rippers
- Augers
Machinery Failure Case Studies
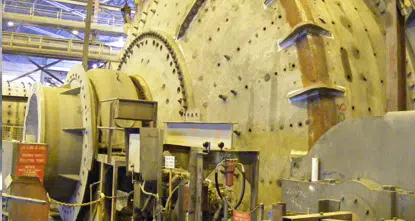
Failure Analysis of a SAG Mill
Towards the end of its service life, a 34ft diameter SAG mill developed cracks in the corner weld. Our engineer inspected the mill. Finite Element Analysis (FEA) was conducted on the shell to determine the reduction in stress intensity at the repaired site. Recommendations were provided for its continuing use and potential replacement.
Our engineer performed a design review of the replacement Mill, including visits to the manufacturer in Pennsylvania, USA; and independent Finite Element Analysis (FEA) of the design. Independent quality assurance during the manufacture of the new SAG Mill components in Turkey and China was then provided as part of the Scope of Works.
Water Pipe Sight Glass at Parliament House, Canberra
A failure occurred in a perspex sight glass fitted to the main fire sprinkler system of the Australian Parliament building. Water released from the fire system caused hundreds of thousands of dollars’ worth of damage to the cabinet room and the Prime Minister’s office. Our engineers inspected the fire system at Parliament House, above the cabinet room. To isolate the cause of the failure, both physical and computer modelling were carried out.
SAG Mill Bearing Failure
Both main bearings on a SAG Mill at a cement factory suffered a catastrophic failure. In addition to analysing data on the service life of the bearings, our engineer inspected the SAG Mill and the failed bearings. Our engineer also performed Finite Element Analysis (FEA) to investigate the design of the bearings and bearing housings and the effect of temperature differentials on the thermal expansion of both the bearings and housings. Based on our analysis and computer simulations, Gilmore Engineers were able to advise on the most probable cause of the bearing failures.
Prime Mover Engine Failure
A prime mover driver pulled his rig off the road when he heard unusual engine noise. Subsequent inspections indicated the engine had suffered catastrophic lower connecting rod bearing failure. Our engineers inspected the engine to determine if the engine had consumed or leaked a large quantity of engine oil, which may have led to the failure.
Drill Rig Continual Maintenance
After a history of failures, four drill rigs were reviewed. Issues involving the pneumatic system, compressor shaft, cooling system and overheating were identified and detailed. A determination was made as to whether these failures were due to design, manufacture or operator error.
Propeller Bearing Failure
The gearbox of a vessel failed catastrophically. The vessel was docked and the gearbox removed and replaced. However, the stern tube developed a substantial leak on the subsequent trip. On inspection, it was that determined that the bearing had melted. Our engineer reviewed the evidence and provided expert opinion on the cause and timing of the bearing failure.
Failure Analysis of a Girth Gear
A gold mining company contracted Gilmore Engineers to review a mill girth gear failure and the numerous reports that had previously been written regarding its repair. Gilmore Engineers produced a management-level report analysing the failure and providing a recommendation for the potential remaining life of the gear.
Truck Differential Yoke Failure
An underground mine concrete truck impacted a wall on a relatively steep decline. Concern as to whether the truck’s brakes or driveline had failed, or operator error was responsible was investigated. Our engineer determined the cause of failure and provided an expert report for the court.
Rock Hammer Accelerated Wear and Failure
In 2013, Gilmore Engineers inspected a series of failed rock hammer components. Based on visual inspection alone, various failure methods were able to be ruled out, resulting in a renewed focus on the likely remaining causes of failure.